- Industries
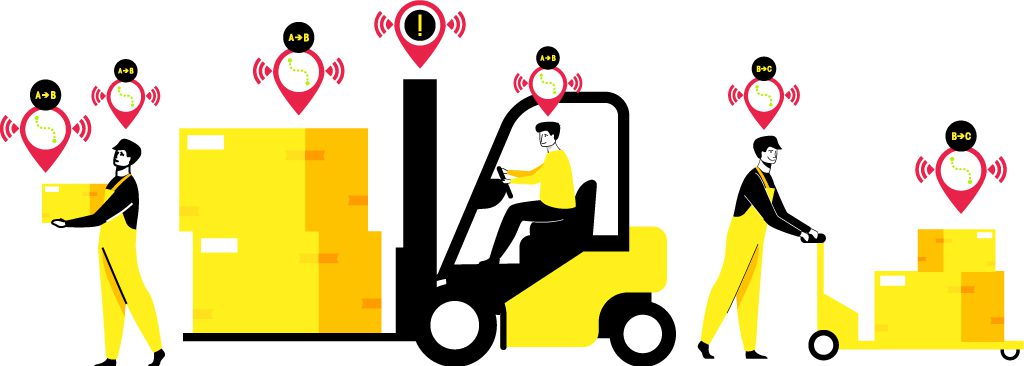
Industrial sites are on a quest for automation and digitalization and you can speed up this transformation with Noccela’s s RTLS technology and expertise. While a lot is being talked about Smart Factory, Industry 4.0, and LEAN processes, it may be difficult to determine how to best get started with digitalizing operations. The solution is easy to deploy with one or two functions and expand on the way as the vision matures. Commonly used starting points of our customers have been forklift tracking, automated (paperless) work orders, first-in-first-out automation, and logistical challenges of tracking assets.
Digitalization of production processes and workflows with rule-driven location capabilities help optimize any production environment. Waste less time, uncover duration of process stages, or trigger events based on location of the products and assets, and other real-world conditions.
- Digitalize product, asset and staff locations to improve visibility of information.
- Monitor and analyze the production flows and identify operational and supply bottlenecks.
- Reduce assembly line pauses with digital Andon feature.
- Reduce shrinkage.
- Shorten lead times with digital work orders.
- Ensure the accuracy and consistency of manufacturing.
- Locate inventory and products easily without wasting time for searching.
- Automate production status and progress calculation.
Knowing the exact location of the pallets and packages unleashes tremendous benefits for Logistics centers and warehouses in everyday operations. The goods are no longer lost for days and tracing investigations have never been easier. The warehouse operations can be optimized, improving the delivery lead times and quality of the service levels.
- Enable track and trace of assets across facility map in real-time.
- Generate utilization and productivity KPIs with greater business value.
- Optimize the warehouse layout for better efficiency and convenience, based on facts.
- Take control over costs by recognizing the occurrences of instantaneous bottlenecks and corresponding solutions.
- Diminish delays with automated First- In First- Out (FIFO) practices.
- Maintain Forklift safety using dynamic danger zone definition.
- Save tracking costs of thousands of palettes by tracking only the moving vehicles.
One of the main categories of workplace accidents is related to man-to-machine proximity. Forklifts and dangerous industrial utilities are responsible for a surprisingly large share of the incidents, and the severity of injuries goes up to death. Besides the damage on life, assets, and operations, the compensative costs to the organizations are constantly increasing. Thereby, the improvement of preventive action against accidents can eliminate or minimize the risk level, improve worker safety and increase Return on Investment all together.
- Enable tracking the workers, and dangerous assets and utilities for safety purpose.
- Define dynamic/fixed danger zones around dangerous assets and utilities which could be moving or non-moving.
- Alert workers if they come across the danger zones.
- Alert operators if other workers are in proximity of the dangerous assets they are operating.
- Detect lone-workers to call for assistance automatically.
- Enable smart evacuation feature to gain visibility of actual evacuation flow and for automatic roll-calling at muster stations.
- Generate Safety KPIs for continuous comparison with the goals and improving safety practices.